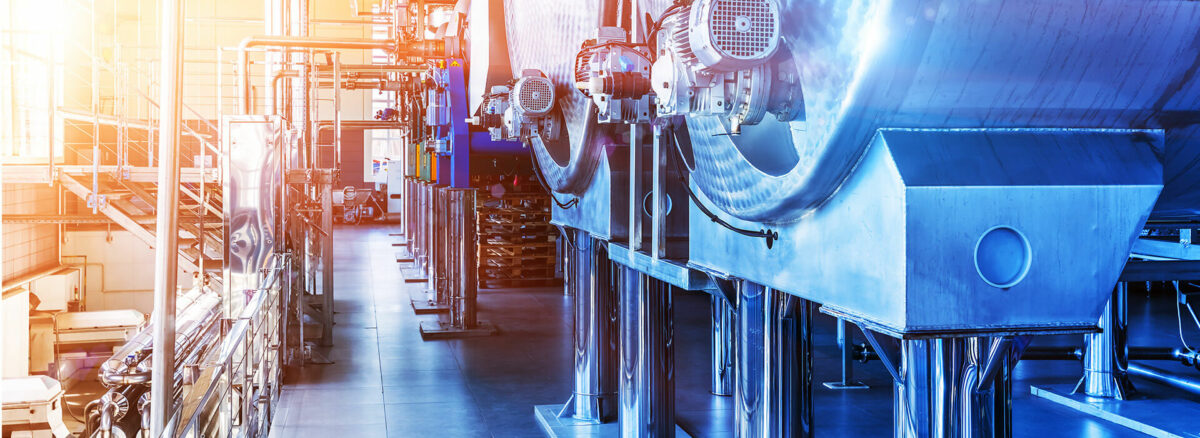
How Manufacturers Can Operate Safely and Productively During the COVID-19 Crisis
The coronavirus (COVID-19) pandemic has forced American businesses to adapt quickly to a radically new economic and operating landscape. If your company sells, manufactures, delivers, distributes or otherwise facilitates goods considered “essential” you may need to operate at full (or overtime) capacity. On the other hand, manufacturers whose goods aren’t deemed essential may be forced to idle their machines and close their doors indefinitely. (In many cases, state guidelines specify which businesses are essential and which ones aren’t.)
Both situations are challenging. But if you’re up and operating, here are four considerations to help you do so safely and productively:
1. Keep Workers Safe
The health and safety of workers has always been a priority for manufacturers. Now you must contend with the threat of COVID-19. If some of your employees can work from home, enable them to do so successfully by ensuring they have the technology and other resources they need. Even as states “open for business” again, consider keeping remote workers at home, if possible, until COVID-19 treatments or a vaccine are available.
For workers who must be on-site, consider scheduling skeleton crews in shifts and try to keep the same workers on individual crews to limit potential exposure. Also limit the number of managers working at any one time in production areas. Even if you normally operate nine to five, the transition to 24-hour operations may be easier than you think. Exercising flexibility helps lower the risk that the virus might spread. And if an employee does become sick, fewer coworkers will be required to self-quarantine.
Positive cases of COVID-19 exposure should be treated seriously. In addition to quarantining workers, you must thoroughly clean all production and office areas before allowing operations to resume.
2. Embrace Innovation
Doing things the way you always have may not be the best course right now. Instead, be ready to adapt and innovate whenever the situation calls for a different approach. For example, most manufacturing workers don’t work from home. But 3D printers may make it possible for some employees to produce goods while social distancing.
Or consider how your company might repurpose goods to meet new demands. As has been well-publicized, some companies are redeploying resources to produce ventilators and other needed medical equipment. In many cases, manufacturers may find it relatively easy to pivot to new production modes and goals. For instance, some distilleries are converting alcoholic beverages into disinfectants. Paper producers might ramp up production to meet increased demand for shipping boxes. And manufacturers already producing cardboard could redesign templates to make more “to-go” boxes for restaurants that have been forced to close dining areas.
Be sure you heed federal and state government mandates. Some companies may be asked to modify their operations so they can produce in-demand medical or cleaning products. Even if you aren’t required to change your operations, look for opportunities to address the current situation. Slight alterations could mean the difference between your products being deemed essential vs. non-essential. If you’re a link in an important supply chain, you may be able to make the case for continuing operations.
3. Plan for Financial Challenges
Your factory may be busy now, but there’s no guarantee that will be true in a few months. The financial ramifications of COVID-19 could be long-lived — and dire — for many businesses. Plan so that work slow-downs don’t sneak up on you.
Federal and state authorities have introduced various tax breaks, particularly for companies that keep workers on the payroll. The Families First Coronavirus Response Act made certain employers eligible for tax credits so long as they provide paid sick leave to COVID-19-positive employees or workers who have to stay home to care for sick family members.
The subsequent Coronavirus Aid, Relief, and Economic Security (CARES) Act authorized several provisions, including:
- Delays for payroll tax obligations,
- An employee retention credit,
- Favorable tax provisions for businesses incurring losses, and
- Expanded unemployment benefits for workers.
The CARES Act also launched the massive Paycheck Protection Program (PPP) that offers qualified businesses forgivable loans and other forms of relief for keeping employees on the payroll. After the available money ran out, Congress approved a second round of funding for the PPP in late April.
State and local support levels vary depending on the municipality. For example, your state may have removed some restrictions for businesses producing essential products.
4. Get Professional Advice
Your manufacturing management team doesn’t have to tackle the many challenges of the COVID-19 crisis alone. We have up-to-date information on federal and state benefits available to manufacturers. And we can help you navigate the lending landscape. For example, we can help identify appropriate lenders and prepare the calculations and statements required to apply for PPP loans. Don’t hesitate to contact Yeo & Yeo’s manufacturing advisors.
The information contained in this post may not reflect the most current developments, as the subject matter is extremely fluid and constantly changing. Please continue to monitor Yeo & Yeo’s COVID-19 Resource Center for ongoing developments. Readers are also cautioned against taking any action based on information contained herein without first seeking professional advice.